ALLISS Aerosystems Lesson Learned Information Sharing System
The ALLISS is a Lessons Learned Database is a knowledge repository system which helps Aerosystems users capture, store and manage experiential knowledge from projects, events or operations.
Use of lessons learned is a principal component of an organizational culture committed to quality, continuous improvement and adaptive management. Lessons learned mechanisms communicate acquired knowledge more effectively and ensure that beneficial information is factored into planning, work processes, and activities.
Features such as reports, categorization tools and search functionality serve to help users manage company knowledge for future reference. With this webpage, users have the flexibility to access information on the move from any desktop, laptop, smartphone or tablet.
The ALLISS Lessons Learned Database allows Aerosystems employee to capture knowledge via online form, in which users can enter a lesson description, title and recommended actions, as well as add comments and attachments. To help ensure data quality, ALLISS supports content validation through a review process made by the Quality Assurance Team before publishing.
All Aerosystems teams, people and departments are welcome to use ALLISS.
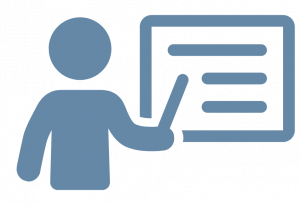
ID1 - BONDING TIPS
SITUATION: During the ATP of Cockpit Fans the Bonding value is difficult to reach.
LESSON LEARNED AND RECCOMENDATIONS:
In some cases (products) the Bonding Value Requirement is very low and to obtain this it is necessary to have a good live contact between metal parts. In order to have a live contact it is necessary to use a compound between parts (like Silver).
It is reccomended to use Conductive Adhesive (Ref. CHO BOND) in order to reach the corrected value, not only for the fans but also for each bonding requirement (and also to use a Vice during test).
It is reccomended that all technicians to follow the Bonding Course ASC012 (one time).
Engineering: to set the use of Conductive Adhesive in Drawings and BOMs.
Production: to specify in CDLs the use of Conductive Adhesive.
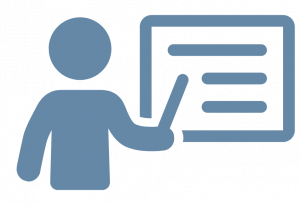
ID2 - TEST EQUIPMENT AVAILABILITY
SITUATION: During the development of the new product (eg. Gravity Filler Cap) the Test Equipment (Kart Oil tank) was not able to contain the pressure of the cap. The definitive tank was not ready (designed and manufactured) at the date of the test.
LESSON LEARNED AND RECCOMENDATIONS:
It is reccomended that all Test Equipment must be developed, manufactured and provided BEFORE the start of the tests. Included also in the MPP. The ATE must be designed as a final assy (project) completed with accessories, parts, tools and any other needs.
Production: to specify in CDLs the use of Conductive Adhesive.
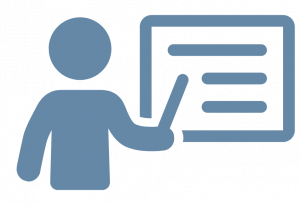
ID3 - THREE "I" RULE
SITUATION: During the project of new products (eg. Potentiometers) the Installation was not checked and for this reason the procedure was difficult due to a different machining of the shaft.
LESSON LEARNED AND RECCOMENDATIONS:
It is reccomended that during the development phase the engineering must check the following: THREE "I" RULE.
To Check and See the real Item actually used by the customer in order to discover differences and problems.
To Check and See the real actual installation of the item to verify needs.
To talk with the installer in order to have a feedback on the item installation problems and use (also safety).
The Engineering dept. must alert the commercial dept. in order to have: the Item actually used, the meeting to check Installation and to talk with the Installer.
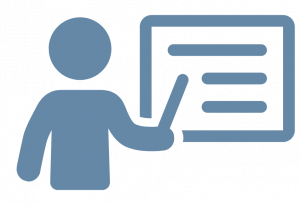
STOCKED MATERIALS
SITUATION: Due to unique supplier of a component (ex. Wiper Blade, tachometer Case etc.) and for avoid long delivery and obsolescence or discontinuation
LESSON LEARNED AND RECCOMENDATIONS:
It is reccomendend to find a DUAL SOURCE (if possible) and/or to buffer stock with previsions on future quantities (ref. EN9134)
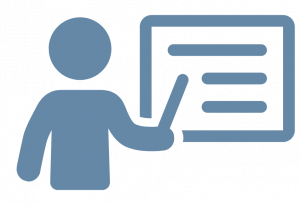
PRODUCT MOCKUPS
SITUATION: During the first assembly of a new product, we realize that some problems not noticed in the design phase.
LESSON LEARNED AND RECCOMENDATIONS:
Thanks to 3D printing it has been possible to minimize the problems in question, but it is still not enough. It emerged that some small problems (which in any case do not affect the functionality of the product) emerge after a few days of assembly and use tests. Unfortunately, after the release of the construction drawings it is not convenient to delete them. The recommendation is to create mockups well in advance, using materials and dimensions of the drawing so as to be able to gain confidence and thoroughly stress the parts with the aim of bringing out most of the problems.
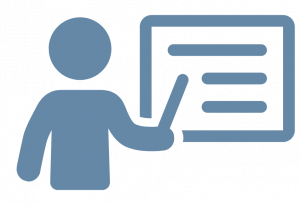
ROTOR MOLDS
SITUATION: During the compression of Rotor Windings it is needed a special double mold in order to be conform to the final dimensions (envelope) of the rotor and to prevent shorts.
LESSON LEARNED AND RECCOMENDATIONS:
It is reccomended during the design steps to draw the Double Rotor Molds in the CAD 3D Model and to issue a drawing. The Mold shall be made in appropriate materila in order to prevent shorts during the compression phase. The molds needs to be mada and availabel before the first batch prodcution of any Rotor PN.
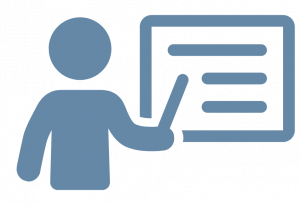
CPCP HARMFUL PRODUCTS
SITUATION: Some product were find with the use of prohibited harmful products (corrosion inhibitor compound).
LESSON LEARNED AND RECCOMENDATIONS:
It is reccomended during the design steps to verify and select only chemical products that are not harmful to humans by the review of TDS and SMDS (and to be included in the Material Analysis and into the MPP).
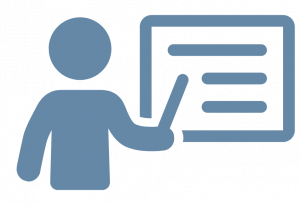
CPCP USE OF NON CORROSIVE METALS
SITUATION: Some products were find with the use of Corrosive Metals (steels and irons) that were find partially rusted.
LESSON LEARNED AND RECCOMENDATIONS:
It is reccomended during the design steps to verify and select only Non Corrosive Materials (Stainless Steel Metals) that are approved for the use in the aerospace manufacturing (and to be included in the Material Analysis and into the MPP).
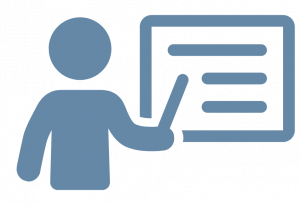
O-RINGS VERIFICATION
SITUATION: Some O-Rings were found damaged
LESSON LEARNED AND RECCOMENDATIONS:
It is reccomended during the design steps to verify and select only FLUIDS COMPATIBLE O-Rings and eventually testing.
Lesson Learned Submission Form
This Lesson Learned Submission Form provides a simplified format to capture these experiences in an effective manner.
Instructions:
The ALLISS system is designed to stimulate employees who live daily in the company to identify any Lesson Learned to be captured and shared.
The use of the Lesson Learned Submission Form is very simple, since it is sufficient to fill in the mandatory fields indicated with an asterisk, briefly describe the SITUATION (context), the LESSON LEARNED and the RECCOMENDATIONS; after completion of all fields send the form with the submit button.